Une station de vidange de Big Bags et un convoyeur à vis flexible alimentent une extrudeuse à deux vis dans un espace restreint
WOONSOCKET, RI — Le groupe Plastics of America mélange des thermoplastiques dans un vieux moulin à Woonsocket, RI. Lorsque l'entreprise a cherché à augmenter sa capacité grâce à des lignes de mélange à deux vis au lieu de lignes à vis unique, les plafonds relativement bas du bâtiment ont affecté la disposition de l'équipement. Mais grâce à une planification minutieuse et à l'utilisation d'équipements de déchargement et de convoyage de Big Bags, l'entreprise a été en mesure de tout installer sur un seul niveau de son bâtiment de 5 574 mètres carrés.
L'histoire commence en 2001, avec la décision d'ajouter sa première extrudeuse à deux vis de 68 mm de diamètre pour le mélange. (Ce projet s'est concrétisé en 2002.)
«Nous avons une hauteur sous plafond limitée dans l'usine — de 4,2 à 4,8 m», explique Duane T. Delaney, directeur technique de The Plastics Group. L'extrudeuse et l'équipement auxiliaire devaient tenir dans cet espace. Une option était de découper dans le plafond. Mais M. Delaney pensait que cela ne permettrait pas d'améliorer l'efficacité et, surtout, la sécurité des travailleurs car il faudrait ajouter des plates-formes pour accéder aux équipements auxiliaires tels que les trémies qui alimentent l'extrudeuse. Au lieu de cela, il a conçu une ligne de mélange où tout l'équipement tient sur un étage.
M. Delaney n'aime pas les plates-formes à plusieurs niveaux de la plupart des lignes à deux vis équipées d'alimentateurs et d'autres systèmes auxiliaires. «Elles s'élèvent à 6 à 9 m, rendent difficile et dangereux le nettoyage et l'entretien de l'équipement, et ajoutent 100 000 $ à 200 000 $ au coût d'une ligne de mélange pour les plates-formes, les rampes et les marches», explique-t-il.
«Notre philosophie de production est de faire en sorte que les opérateurs puissent faire leur travail sans danger, simplement et facilement» ajoute M. Delaney.
Protéger les propriétés des additifs
Les quatre trémies de résine de l'extrudeuse à deux vis sont alimentées par des lignes pneumatiques à partir de silos. Le système d'alimentation de l'additif, cependant, était un défi puisqu'il devait répondre à plusieurs critères en dehors de la restriction de hauteur. The Plastics Group utilise de nombreux additifs, charges et renforts, comme le talc, le mica, le carbonate de calcium et le sulfate de baryum et même des fibres de verre et des perles. Le transport d'additifs et de charges en poudre vers un alimentateur à partir d'un endroit éloigné par un système pneumatique ou mécanique signifierait un coût relativement élevé pour le convoyeur et l'installation, ainsi que l'entretien plus intensif associé aux types de systèmes de convoyage plus longs. Le transport de fibres de verre sur de plus longues distances augmenterait également la possibilité d'endommager le matériau, ce qui affecterait les propriétés du composé.
M. Delaney a décidé que la solution était un système de déchargement de Big Bags associé à un convoyeur à vis flexible à faible coût et à maintenance réduite installé près de la ligne de mélange. La station de vidange vide les Big Bags dans une trémie à sa base, et le convoyeur à vis flexible transporte les additifs à travers un tube incliné jusqu'à un alimentateur sur la ligne de mélange.
En raison de l'emplacement de l'extrudeuse à deux vis, M. Delaney explique, «la station de vidange de 4,7 m de haut ne pouvait être installée qu'à un seul endroit et l'alimentateur d'additif à deux vis ne pouvait être rempli qu'à un seul endroit. Il est devenu évident qu'un convoyeur à vis flexible était un système simple et direct répondant à tous nos besoins».
Cette installation était également plus efficace — et plus sûre — que si les travailleurs ouvraient et vidaient manuellement des sacs de 22,7 kg d'additifs dans la trémie d'alimentation à partir d'une plate-forme. Avec cet ancien processus, on risquait d'introduire des déchets de sacs et d'autres contaminants à l'opération de mélange, on mangeait de l'espace au sol pour l'entreposage des sacs et il subsistait un problème coûteux d'élimination des sacs vides devenus des déchets.
L'intégration de la station de vidange de Big Bags et du convoyeur à vis flexible a permis de transporter rapidement les charges ou les renforts vers l'alimentateur d'additif. «Les extrudeuses ont chacune cinq systèmes d'alimentation par gravité». L'un est pour les additifs et les autres pour les résines. «Le matériau doit être transporté vers l'alimentateur d'additif assez rapidement pour maintenir un dosage précis», dit-il. Une charge d'additif de 45,3 kg, par exemple, doit être acheminée de la trémie de déchargement à l'alimentateur en 10 secondes. Un système de contrôle de perte de poids démarre et arrête le convoyeur à vis flexible lorsque la trémie d'alimentation atteint des niveaux de poids prédéfinis.
Relier la station de vidange de Big Bags et le convoyeur à vis flexible a si bien fonctionné que lorsque The Plastics Group a eu besoin d'une deuxième ligne à deux vis, en 2007, d'une unité à grande vitesse de 70 mm de diamètre (lancement en 2008), il a commandé une autre station de vidange de Big Bags et un convoyeur à vis flexible.
La station de vidange de Big Bags a de multiples caractéristiques
Pour les deux installations, la société a choisi la station de vidange de Big Bags BFC. Les sacs sont attachés à un berceau de levage à quatre coins à profil bas avec des fixations de sangle de sacs Z-CLIP™ et positionnés grâce à un chariot élévateur électrique monté sur une poutre en I en porte-à-faux.
Une vanne de réglage de débit POWER-CINCHER™ pneumatique régule le débit à travers la manchette du sac. Ceci est fait par une série de tiges courbes et articulées en acier inoxydable qui serrent la manchette de façon concentrique sur un axe horizontal pour la fermeture et sur un axe vertical pour éviter les fuites de matériau. La vanne permet également de refermer la manchette si un sac est partiellement vidé.
La station de vidange BFC est équipée d'un collier de serrage SPOUT-LOCK™ qui connecte la manchette du Big Bag à un tube télescopique TELE-TUBE™. Le tube maintient une tension vers le bas sur le collier de serrage, gardant la manchette tendue et empêchant le matériau de créer des renflements ou de s'accumuler à l'intérieur pendant la déchargement et de créer des restrictions de débit.
Les deux stations de vidange de Big Bags ont deux plaques d'agitation FLOW-FLEXER™ pneumatiques qui soulèvent et abaissent le fond d'un sac pour maintenir un débit positif et obtenir un déchargement complet.
The Plastics Group commande habituellement des sacs de 453 à 1 132 kg. Certains additifs qu'il utilise sont expédiés dans des sacs de 1 359 kg, de sorte que les stations de vidange de Big Bags BFC sont conçues pour supporter des charges de 1 812 kg.
Le convoyeur à vis flexible d'origine a un diamètre de 150 mm, est installé à un angle de 35 degrés et transporte le matériau sur 5,2 m jusqu'à la trémie d'alimentation. M. Delaney dit que lorsque la vis flexible tourne, elle s'auto-centre à l'intérieur du tube extérieur en polymère, ce qui permet d'acheminer efficacement le matériau vers les alimentateurs sans endommager les fibres de verre et autres renforts.
Le deuxième convoyeur à vis flexible a un diamètre de 115 mm, et s'étend sur 8,4 m à un angle étroit pour vider le matériau dans l'alimentateur d'additif de l'extrudeuse à deux vis.
M. Delaney dit que les convoyeurs à vis flexibles, tous deux de Flexicon, manipulent chacun 22,7 à 907 kg par heure d'additifs selon le matériau à mélanger. L'entreprise change de matériau une ou deux fois par jour en moyenne. Un cycle typique dure 18 heures.
Le système d'alimentation est fiable
Les stations de vidange de Big Bags BFC et les convoyeurs à vis flexibles ont fonctionné presque sans faille. «Nous n'avons eu à faire que l'entretien normal», dit M. Delaney.
La fiabilité est essentielle aux opérations. «Si l'un ou l'autre de ces systèmes tombe en panne, il n'y a pas de remplacement». Et sachant que chaque ligne est capable de mélanger 31 710 kg par heure, un système de déchargement moins fiable et un système de convoyage à vis flexible pourraient créer des problèmes de production majeurs.
The Plastic Goups ne publie pas de chiffres d'affaires, mais M. Delaney indique que le marché est suffisamment important du point de vu des clients finaux pour que les ventes soient restées stables même pendant la récession. L'entreprise fournit du polypropylène chargé et renforcé, ainsi que des polyoléfines recyclées, du polystyrène choc et de l'ABS, pour l'automobile, les loisirs, l'emballage, la construction, les appareils électroménagers, les jouets, les biens durables et d'autres applications.
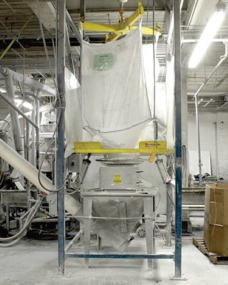
En savoir plusThe Plastics Group a installé sa première station de vidange de Big Bags et son premier convoyeur à vis flexible pour transporter les additifs vers une extrudeuse à deux vis. Le sac est positionné à l'aide d'une poutre en I en porte-à-faux, d'un palan électrique et d'un chariot. Les plaques d'agitation FLOW-FLEXER™ soulèvent et abaissent les côtés inférieurs du sac pour un déchargement complet.
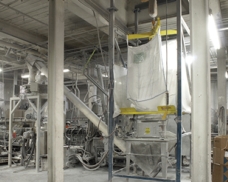
En savoir plusLa première station de vidange de Big Bags installée par The Plastics Group est reliée à un convoyeur à vis flexible de 150 mm de diamètre qui transporte le matériau sur 5,2 m vers une trémie d'alimentation sur une extrudeuse à deux vis.
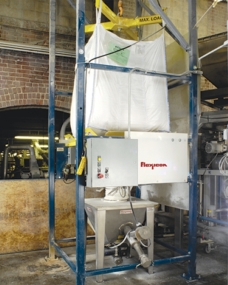
En savoir plusLa flexibilité de l'acheminement des lignes de convoyage a permis à The Plastics Group de positionner deux stations de vidange de Big Bags Flexicon dans des espaces restreints, éliminant ainsi le besoin d'un réseau coûteux de lignes pneumatiques.
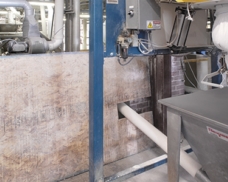
En savoir plusLe convoyeur à vis flexible de 115 mm de diamètre sortant de la deuxième station de vidange de Big Bags traverse une paroi pour atteindre la trémie d'additif sur l'extrudeuse, surmontant ainsi les contraintes d'espace.
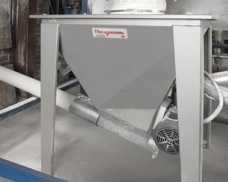
En savoir plusChaque station de vidange de Big Bags vide l'additif dans une trémie, qui utilise un vibrateur à turbine pneumatique et un agitateur mécanique pour favoriser le débit du matériau dans l'entrée du convoyeur à vis flexible.
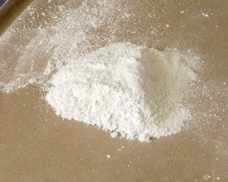
En savoir plusBon nombre des additifs manipulés sont des poudres qui seraient difficiles et coûteuses à transporter sur de longues distances à travers l'usine.
X-0823