Le système de manutention de Big Bags réduit les stocks de noir de carbone et maintient la ligne de mélange propre
BREA, CA — Le fabricant d'élastomère Kirkhill-TA Co. a réduit ses stocks de noir de carbone et amélioré la propreté de son usine en remplaçant un grand système de stockage en silo par un système de déchargement de Big Bags BULK-OUT® de Flexicon. Il a permis à l'entreprise de réduire ses stocks de 90 %, tout en empêchant la poussière de noir de carbone de contaminer l'environnement de l'usine. Les économies de coûts et l'amélioration de l'efficacité et de la compétitivité sont d'autres avantages de ce système.
Le système de manutention de matière vrac est la dernière nouveauté pour cette entreprise qui a commencé à fabriquer des joints et d'autres produits en élastomère en 1919, et a graduellement déplacé la production de produits industriels généraux vers des pièces en silicone hautement techniques pour les avions commerciaux et militaires, les missiles et même la navette spatiale américaine.
Le noir de carbone est l'un des principaux matériaux transformés de Kirkhill-TA. L'ajout de noir de carbone à un élastomère réduit son taux de dilatation thermique, ce qui lui permet de maintenir une étanchéité à l'air dans les applications à haute température. Il peut également modifier l'allongement, la rigidité et d'autres propriétés physiques et transmettre une conductivité pour prévenir les décharges statiques.
Comme Kirkhill-TA est passé d'une production de masse de pièces industrielles à une production de pièces aérospatiales à plus faible volume, il est devenu inutile et coûteux de maintenir des stocks de noir de carbone dans des silos. «Avec les wagons, nous devions apporter 136 363 kg de pellets de noir de carbone à la fois», a déclaré Larry Pierce, vice-président de la technologie d'Esterline. «Nous ne recevions des livraisons que quelques fois par an, et nous accumulions près de 250 000 $ de stock à chaque livraison».
De plus, la ville de Brea a décidé de supprimer la voie ferrée qui alimentait l'usine pour agrandir son parc. «Nous étions la dernière installation industrielle de la ville, et nous étions d'accord», dit Pierce. «En échange, la ville nous a accordé un prêt pour acheter le nouveau système de déchargement de matière vrac».
De plus, la société mère de Kirkhill-TA, Esterline Technologies, a mis l'accent sur le contrôle des coûts des stocks.
Kirkhill-TA avait plusieurs priorités pour son nouveau système de manutention. Il devait améliorer le rendement des stocks et limiter les coûts. Il devait utiliser partir de l'infrastructure existante et l'exploiter au maximum. Enfin, il devait empêcher la poussière de noir de carbone, causée par le frottement des pellets friables entre-eux, de s'échapper dans l'atmosphère de l'usine ou le matériel de traitement.
Le noir de carbone est produit en brûlant du pétrole lourd ou du goudron pour former des particules de suie. Lorsqu'elles sont présentes dans l'air, elles peuvent pénétrer dans le matériel de traitement. «Le noir de carbone a tendance à absorber l'huile lubrifiante», explique M. Pierce. «S'il entre dans les roulements et les rouleaux, ils s'useront prématurément». Il peut également provoquer des courts-circuits.
Le noir de carbone étant un produit pétrolier, il est considéré comme une matières dangereuses en Californie . Bien que le noir de carbone soit expédié sous forme de pellets de 1 à 3 mm de diamètre afin de réduire la probabilité de rejet dans l'air, les fabricants doivent demeurer vigilants afin de prévenir les écoulement accidentels et le nettoyage qui s'ensuivrait.
Un système de wagons gérait la livraison des matières vrac
Kirkhill-TA disposait d'une infrastructure importante pour traiter le noir de carbone, avec une station de déchargement sur rail, y compris des convoyeurs à vis et à godets, et deux silos de stockage.
Les pellets de noir de carbone s'écoulaient des silos vers les mélangeurs Banbury de l'entreprise de deux façons: par convoyeur pneumatique et, lorsque le poids dans le silo était en dessous de 22 675 kg, par de grands bacs en acier qui peuvent contenir environ 909 kg de noir de carbone. «Ce sont comme des sacs en acier. Nous les déplaçons par chariot élévateur et nous chargeons le noir de carbone par gravité dans un conteneur de pesage avec une balance intégrée qui se trouve sur une mezzanine au-dessus des mélangeurs. Lorsque le bac et les pellets atteignent le poids requis pour la recette, la goulotte du récipient s'ouvre, déchargeant le matériau dans le mélangeur pour le mélanger avec des élastomères avant de le mouler en joints finis», explique M. Pierce.
Les convoyeurs pneumatiques ne sont plus utilisés, mais les bacs en acier et le système de pesage font toujours partie de la nouvelle installation de manutention de matière vrac.
Les Big Bags simplifient la manutention
Les Big Bags étaient un choix évident pour recevoir du noir de carbone. Tout d'abord, ils sont disponibles pour les poids allant de 455 et 910 kg, suffisamment importants pour bénéficier de rabais sur les produits en vrac. Bien que les fournisseurs facturent moins cher pour les expéditions de wagons en vrac, les coûts de transport ferroviaire plus élevés annulent ces économies. En changeant de fournisseur, Kirkhill-TA ne paierait qu'une fraction de plus par livre pour les livraisons de Big Bags. Ajoutez à cela les économies réalisées en minimisant les stocks et en éliminant l'entretien des silos, et le système de Big Bag est parfaitement amorti.
La station de vidange de Big Bag Flexicon améliore également la propreté du site. Tout d'abord, elle place les opérations de manutention de produits vrac à l'intérieur de l'installation, de sorte que toute fuite accidentelle est contenue dans l'usine. La station de vidange de Big Bags utilise également des connexions étanches à la poussière pour confiner intégralement le noir de carbone jusqu'à l'ajout final au mélangeur.
Les camions livrent 10 à 12 Big Bags palettisés à la fois. Un chariot élévateur soulève chaque sac par ses sangles et le livre à un site de stockage sur la mezzanine. En cas de besoin de noir de carbone, l'opérateur du chariot élévateur attache les sangles de sac à un cadre de levage de sac détachable, puis soulève le cadre pour le positionner sur les berceaux de la station de vidange de Big Bags.
La station de vidange décharge les pellets de noir de carbone du Big Bag dans une trémie spécialement conçue à cet effet, d'où un convoyeur à vis flexible (également de Flexicon) de 4,5 m de long et 11,4 cm de diamètre extérieur transfère le matériau à un bac en acier. À ce stade, l'opération se déroule comme autrefois avec les bacs en acier ; un chariot élévateur à fourche transporte le bac le long de la mezzanine jusqu'au conteneur au-dessus de l'un des mélangeurs, où il libère sa charge.
Un système étanche à l'air permet d'obtenir une usine plus proper
La station de vidange de Big Bags est conçue pour confiner complètement le matériau déchargé, évitant ainsi la contamination du produit et de l'environnement de l'usine. La manchette de sac est fixée à un collier de serrage SPOUT-LOCK™, qui forme une connexion étanche entre le côté propre de la manchette du sac et le côté propre d'un tube télescopique TELE-TUBE™ (à travers lequel le matériau est déchargé). Le tube soulève pneumatiquement le collier de serrage, ce qui permet à l'opérateur d'établir une connexion étanche à la poussière avec la manchette du sac. Le tube s'abaisse ensuite, allongeant le sac pour décharger complètement les pellets. De plus, les activateurs de sac FLOW-FLEXER™ — deux plaques situées sous le sac — soulèvent et abaissent les bords inférieurs opposés en forme pour leur donner une forme de «V», dirigeant ainsi le matériau vers le manchette du sac.
Au-dessus du collier de serrage, une vanne de réglage de débit POWER-CINCHER™ encercle la partie supérieure de l'embout du sac pour permettre la fermeture des sacs partiellement vides. Lorsque le sac est vide, l'opérateur actionne le collecteur de poussière BAG-VAC™, qui crée une aspiration à l'intérieur du système scellé, ce qui fait que le sac vide s'aplatit (sans émanation de poussière) pour la fermeture et le retrait.
Le convoyeur renferme une vis flexible en acier inoxydable avec une géométrie spécialisée pour minimiser la compression de matériaux comme le noir de carbone qui ont tendance à se comprimer dans les convoyeurs conventionnels.
Lorsque la vis tourne, elle se centre automatiquement à l'intérieur du tube en plastique, laissant un espace suffisant entre la vis et la paroi du tube pour que les pellets puissent s'écouler sans être endommagés.
L'extrémité d'entrée du convoyeur se fixe à la sortie de la trémie. À l'extrémité de déchargement, un moteur de 4 kW entraîne la vis lorsque le matériau passe de la sortie du convoyeur à la trémie en acier en passant à travers un tuyau de descente flexible de 15,2 cm de diamètre. Entièrement hermétique, le convoyeur assure en outre la propreté de l'installation.
Une commande de chronométrage des lots active le convoyeur pendant un intervalle de temps répétable pour remplir le bac.
«Nous avons réduit les stocks de noir de carbone de 227 000 - 454 000 kg à 22 700 - 45 400 kg», explique M. Pierce. «Le système de déchargement de matière vrac améliore l'efficacité et la compétitivité et réduit nos coûts».
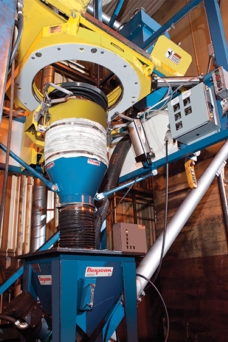
En savoir plus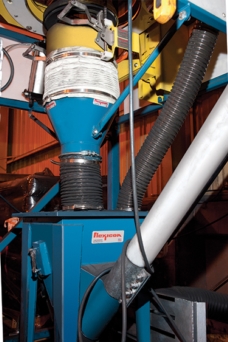
En savoir plusLa station de vidange de Big Bags, la trémie et le convoyeur à vis flexible de Flexicon retiennent les pellets de noir de carbone, empêchant la poussière de pénétrer dans l'environnement de l'usine. Un collier de serrage SPOUT-LOCK™ forme une connexion étanche entre la manchette du sac et le tube télescopique TELE-TUBE™, qui maintient le sac tendu lorsqu'il se vide ou s'allonge, favorisant ainsi le déchargement. Le système hermétique est connecté par le tuyau noir à un collecteur de poussière BAG-VAC™ qui confine la poussière déplacée et aplatit les sacs vides, éliminant ainsi la poussière causée par l'aplatissement manuel des sacs.

En savoir plusKirkhill-TA reçoit du noir de carbone dans des Big Bags pour minimiser les stocks. Le noir de carbone confère des propriétés importantes aux élastomères que Kirkhill-TA fabrique.
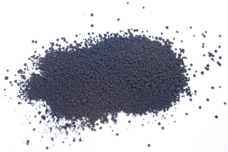
En savoir plusLa poussière est créée lorsque des pellets de noir de carbone de 1 à 3 mm de diamètre se frottent les unes aux autres.
X-0890