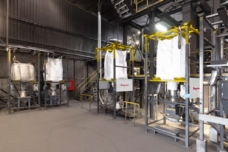
En savoir plus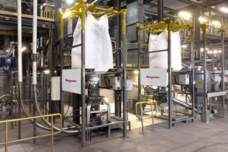
En savoir plusDes paires de déchargeurs de big bags chargés par des chariots élévateurs alimentent en graphite brut des convoyeurs à câbles tubulaires et des convoyeurs à vis flexibles qui l'acheminent vers des silos et le processus de broyage.
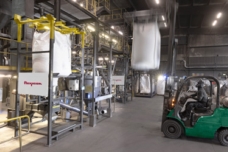
En savoir plus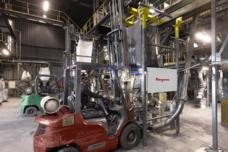
En savoir plusUn chariot élévateur charge le support de levage avec le big bag dans les godets de réception situés au sommet des montants de déchargement.
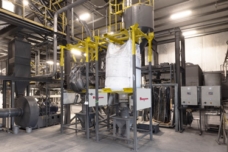
En savoir plus
En savoir plusDepuis les trémies situées sous chaque déchargeur de big bags, des convoyeurs à vis flexibles introduisent le graphite brut dans un convoyeur à câble tubulaire, qui l'achemine doucement vers un broyeur à jet situé sur la mezzanine.
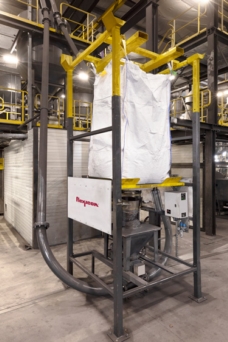
En savoir plus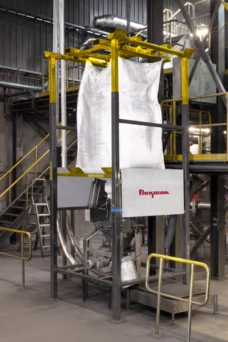
En savoir plusUne vanne rotative située sous chaque trémie alimente en graphite un convoyeur à câble tubulaire, qui l'achemine doucement et sans poussière vers un broyeur à jet pour un broyage fin.
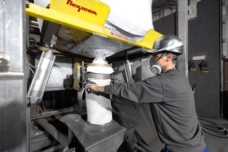
En savoir plusUn anneau de serrage SPOUT-LOCK™ positionné au sommet d'un tube télescopique TELE-TUBE™ applique une tension constante vers le bas à mesure que le sac se vide et s'allonge pour une évacuation complète et sans poussière.
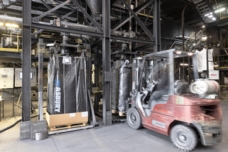
En savoir plusDepuis le silo situé au-dessus, le graphite broyé se déverse en continu dans une paire de remplisseurs de big bags.
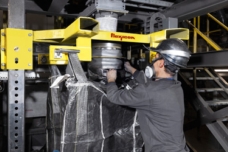
En savoir plusSur la remplisseuse de big bags Twin-Centrepost™, l'opérateur fixe la goulotte du big bag à la tête de remplissage à l'aide d'un joint gonflable afin d'assurer un remplissage sans poussière. La tête de remplissage réglable en hauteur s'adapte à différentes tailles de big bags.
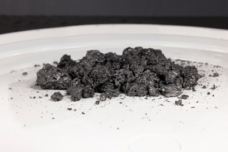
En savoir plusLe graphite brut provient du monde entier.
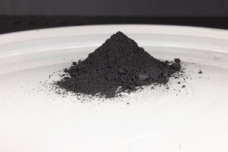
En savoir plusLe produit final d'Asbury Graphite & Carbon.